FOTO I VIDEO Ovako izgleda tvornica na Jankomiru u kojoj Rimac proizvodi Neveru
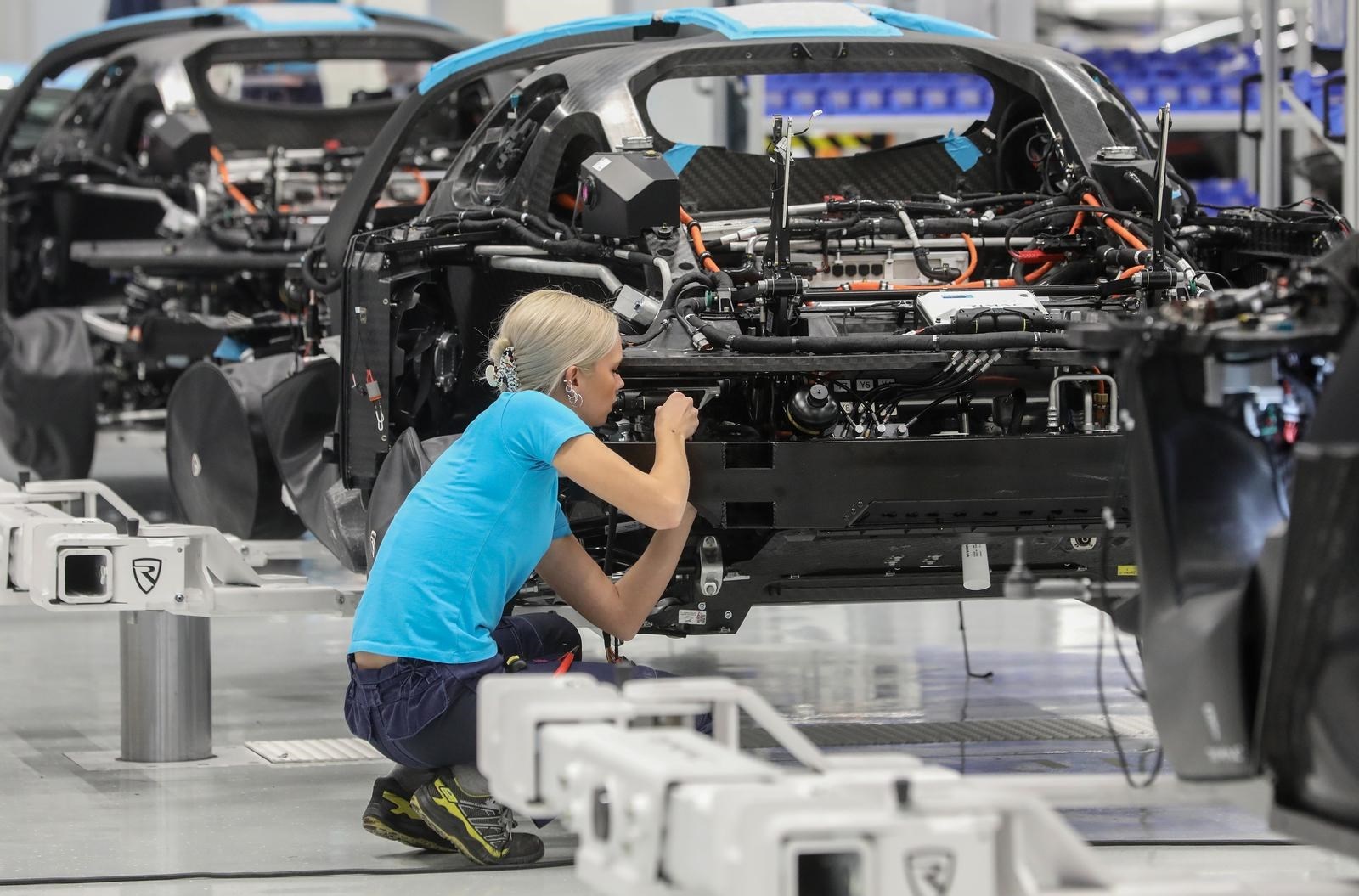
TVRTKA Rimac Automobili pozvala je medije u posjet njihovoj zagrebačkoj tvornici na Jankomiru, gdje su pokazali kako izgleda proizvodnja Nevere. Iz Rimac Grupe su se odmah na početku pohvalili da konstantno obaraju nove rekorde.
"Isporučili smo već više od 400 Bugattija i počeli smo isporučivati Nevere kupcima, od kojih je prvi Nico Rosberg", rekao je Marko Brkljačić, direktor strateških projekata u Rimac Grupi.
Svjetski prvak Formule 1 iz 2016. godine Nico Rosberg svoju je Neveru dobio u kolovozu prošle godine.
"Isporučeno je više od jedne Nevere, 50 ih je prodano"
"Isporučeno je više Nevera, a ostale su u proizvodnji. Zasad je rasprodano 50 automobila, ali nisu još isporučeni", rekla je šefica marketinga i komunikacija Marta Longin na pitanje jesu li isporučili više od jedne Nevere. Bugatti je rasprodan do 2026. godine, kaže.
"Nevera je završena. Nekolicina ljudi ju je isprobala i dobili smo sjajne ocjene. Osvojili smo i neke nagrade", rekla je Longin.
"Već neko vrijeme proizvodimo oko 90 Bugattija godišnje, ali to će rasti. Ukupan broj proizvedenih Nevera će biti 150, ali to ne uključuje nove serije", rekao je Marko Brkljačić.
Ukupni broj automobila koji se godišnje proizvedu, uključujući i Bugatti i Neveru, je 150. "To je naš market potential, moramo ih držati ekskluzivnima", kaže Martina Verović, šefica kadrovske.
Na Neveri je, u nekom obliku, radilo oko 3000 ljudi, ali glavni tim koji je razvio ovaj model se sastojao od oko 200 ljudi. Svi oni trenutno rade na novom modelu Bugattija.
"Naš zadatak je da Bugatti, koji ima veliku bazu kupaca, odvedemo na novu razinu", rekla je Longin. Bugatti-Rimac već posluje u plusu, naglasila je.
"Rimac Automobili su uplatili više u proračun nego što su dobili"
"Mi smo od početka postojanja firme do kraja 2022. godine u državni proračun uplatili preko 44 milijuna eura, a od Hrvatske smo dobili 3.2 milijuna eura. Od Europske unije smo, preko Hrvatske, dobili osam milijuna eura sredstava", rekao je direktor strateških projekta Marko Brkljačić.
Naglasio je i da se ovi brojevi odnose samo na tvrtku Rimac Automobile, a ne i na druge tvrtke poput Project 3 Mobility, koja razvija robotaksije. "Project 3 koji je dobio bespovratna sredstva od skoro 200 milijuna eura je poseban biznis u kojem Rimac Grupa ima udio. To je potpuno odvojena firma", rekao je.
Uz Rimac Automobile, suvlasnik tvrtke je i južnokorejska KIA. Za razvoj robotaksija je kroz Nacionalni plan oporavka i otpornosti osigurano 1.485 milijardi kuna (197 milijuna eura), dok će se ostatak od 3.4 milijarde kuna (451 milijun eura) potrebnih za razvojnu fazu financirati od privatnih investitora, objavili su ranije iz Rimca.
"Mi već imamo ugovorene neke projekte koji će donijeti velike profite, ali oni jednostavno još nisu došli do proizvodnje. Ti prihodi će doći kroz desetke tisuća jedinica koje ćemo isporučiti", rekli su iz Rimca i dodali da su potrebne godine da bi cijela tvrtka ostvarila pozitivne financijske rezultate.
"Mi ćemo morati još puno ulagati da bi postali financijski održiva firma. To ćemo biti, ali to ima svoj put", rekla je Martina Verović, šefica kadrovske.
Cijena osnovnog modela Nevere je oko dva milijuna eura
Rimčeva Nevera u studenom prošle godine postigla je najveću brzinu od 412 km/h, što ju je tada učinilo najbržim električnim serijskim automobilom na svijetu. Godinu dana ranije je oboren još jedan rekord, kada je neovisno potvrđeno ubrzanje Nevere od 8.582 sekunde na četvrtinu milje, što ju je učinilo najbrže ubrzavajućim serijskim automobilom na svijetu.
Cijena osnovnog modela Nevere, bez ikakvih prilagodbi i posebnih zahtjeva, kreće se oko dva milijuna eura, bez poreza.
"25 kilometara žica u svakoj Neveri"
Boris Habulin, koordinator odjela ožičenja, kaže da se gotovo sve ožičenje koje se nalazi u Neveri proizvede u tvornici u Jankomiru te da se gotovo sve radi ručno.
"U autu imamo ukupno oko 25 kilometara žice, 10 tisuća spojeva i tisuću konektora. Sve se radi kod nas, dok druge tvrtke to prepuštaju podizvođačima. To nam omogućava fleksibilnost i lakše uvođenje promjena", rekao je Habulin. Ovaj pristup im je pomogao izbjeći probleme koji su zadesili druge proizvođače nakon izbijanja rata u Ukrajini, zemlji u kojoj se nalazi veliki dio ove industrije.
U Neveru se ugrađuje najkvalitetnija koža dostupna na tržištu, kaže Nikola Đurđek, koordinator tapeciranja. Kupci mogu birati između 38 boja kože, ali moguće je ugraditi i neke druge boje ako to kupac zatraži. Do sada je najčešći odabir kupaca bila crna koža. Za tapeciranje jednog automobila je potrebno do tri tjedna, a potroši se oko 15 kvadrata kože.
"Razvili smo svoje komponente, nismo ih mogli naći na tržištu"
Željko Antunović, koordinator sastavljanja komponenti, kaže da sami proizvode sve elektroničke komponente za Neveru, a pored toga i proizvode za klijente.
"Posebno smo ponosni na pretvarač kojeg, kad smo ga krenuli razvijati, nije bilo moguće naći na tržištu. I danas ih je malo. Ista stvar je s punjačem, tada nije postojao niti jedan koji može izdržati 800-voltnu tehnologiju", rekao je Antunović.
CNC strojevi i izrada kompozita se nalaze u Svetoj Nedelji, dok se ostatak proizvodnje trenutno nalazi na Jankomiru.
"Razvijamo nove baterije, proizvest ćemo desetke tisuća"
"Baterijski paketi koje smo razvijali od 2015., 2016. i 2017. sada se proizvode serijski i nalaze se u automobilima na cesti. Tu se radilo o manjim serijama. Nove baterije koje sada razvijamo naći će se na tržištu za nekih dvije godine", rekao je inženjer proizvodnje Roman Širanović.
Rimac Automobili su počeli surađivati s vodećim imenima u industriji i planiraju serijsku proizvodnju novih modela, kaže Širanović. Plan je proizvesti nekoliko desetaka tisuća baterija, a cijelim procesom bi trebalo upravljati deset do 15 zaposlenika.
Garancija za baterije koje se nalaze u Neveri je tri godine, ali se zbog rjeđeg korištenja ovakvog tipa automobila očekuje da će trajati mnogo duže.
U Neveri se nalazi baterija teška 720 kilograma, duga je preko dva metra i na najširem dijelu široka preko 1.5 metara, kaže Antonio Pokos, voditelj tima sklapanja Nevera baterija. Smještena je iza vozača, duž središnje osi automobila i ispod prostora za noge. Ovaj položaj omogućava niže težište i pravilnu lokaciju centra ravnoteže automobila. Nalazi se u kućištu koje je otporno na vodu i otvoreni plamen.
Veliku većinu testova koji se provode na baterijama, ali i na drugim komponentama, Rimac Automobili provode samostalno. Izuzetak su neki dugotrajni testovi, poput onog za izdržljivost baterije koji traje oko godinu dana.
"Uskoro ćemo sami proizvoditi karoserije"
Na karoseriju koju dobiju od dobavljača u tvornici postavljaju ostale komponente, kaže Ivan Fumić, voditelj proizvodnje hiperautomobila. Nakon preseljenja na kampus, Rimac planira samostalno proizvoditi karoserije, no trenutno za to nemaju prostora, kažu.
U ovoj fazi proizvodnje se provjerava i odgovaraju li dimenzije svih panela, a zatim se ponovno sve rastavlja i šalje na lakiranje. Cijeli postupak sklapanja traje oko tjedan dana.
Za sklopiti jedan automobil potrebno je oko pet tjedana. To, naravno, ne uključuje proizvodnju komponenti.
Boju automobila određuju kupci, a u Rimcu kažu da mogu izmiješati bilo koju nijansu koju kupac poželi. Najčešće su ipak crna, siva, plava i crvena. Posebne boje rezultiraju s višom cijenom i dužim vremenom proizvodnje.
"Kvaliteta izrade i sam osjećaj auta moraju biti na najvišoj razini"
Nakon sklapanja, vozila odlaze u odjel kontrole kvalitete. Kroz taj odjel prolaze i pojedinačne komponente, ali i dovršena vozila.
"Postoji nekoliko faza prije nego što auto bude spreman za isporuku. Auto mora ispuniti dizajnerske i inženjerske specifikacije, imamo i hrpu homologacijskih specifikacija i regulativa. Kvaliteta izrade i sam osjećaj auta moraju biti na najvišoj razini", rekao je Aleksandar Pavlov, voditelj tima za inspekciju kvalitete.
U statičkom dijelu inspekcije se provjerava geometrija kotača, upravljanja, softvera i svake od 500 funkcija u automobilu, kao i položaj panela.
"Auto je opremljen s 12 ultrasoničnih senzora i 13 kamera. U ovom dijelu proizvodnje testiramo i kalibriramo i njih", kaže Pavlov.
Nevera se testira i u komori koja simulira monsun, a gdje se provjerava hoće li nakon 20 minuta unutrašnjost automobila i dalje biti suha. Nakon testiranja kočnica, automobil se testira na cesti. Prije izlaska na cestu se vidljive površine automobila prekrivaju folijom, što može potrajati cijeli dan.
Nevere se testiraju na stazi u Mičevcu, ali i na prigradskim cestama. Centar Zagreba izbjegavaju zbog velike pažnje koju ovaj automobil izaziva u javnosti, kažu iz Rimca. Cijeli proces kontrole kvalitete traje od jednog do dva tjedna.
"Tu ne smije biti nikakvog kompromisa, auto mora biti iznad očekivanja kupca", kaže Pavlov.
"40% zaposlenika su stranci, u Francuskoj ih imamo 150"
Rimac Automobili otvorili su nedavno izložbeni prostor u Bruxellesu u Belgiji, zajedno sa svojim prodajnim predstavnicima za područje Belgije i Luksemburga, tvrtkom D’Ieteren.
"Prošle godine smo narasli za 700 zaposlenika, 550 u Rimac Technologyju i 150 u Rimac Automobilima. Mi smo u fazi da sada pripremamo i uskoro ulazimo u tzv. SOP, state of production, za velike klijente. Tada će Rimac imati veći prihod. Postavljamo prve proizvodne linije za velike kupce", rekao je Brkljačić.
Martina Verović, šefica kadrovske, kaže da u Rimac Grupi 89% zaposlenih radi u Hrvatskoj, 8% radi u Francuskoj, a ostalo su mali uredi na drugim lokacijama.
Spajanjem s Bugattijem Rimac Grupa je dobila novih 150 zaposlenika iz Francuske. Oko 40% zaposlenih u Rimac Grupi su stranci, dok samo u Hrvatskoj je taj broj nešto manji i kreće se oko 30%.
"Mi imamo zaista puno stranaca, brojčano je to oko 700. Međutim, nama je većina radne snage i dalje iz Hrvatske", rekla je Verović i dodala da su većina zaposlenih inženjeri, ali njihov udio u ukupnom broju će se smanjiti kako ukupni broj zaposlenih bude rastao.
"Dobili smo i nagradu za najboljeg poslodavca u proizvodnji i drugi smo najbolji u ukupnom poretku u Hrvatskoj. Mi smo zapravo u konkurenciji s top tri tvrtke koje imaju u prosjeku 250 ljudi. Mi smo jedini koji imaju više od 2000 ljudi, što je velika razlika", rekla je šefica kadrovske.
"Izgradnja kampusa je pri kraju"
Rimčev kampus u Svetoj Nedelji je pod krovom i trenutno se završavaju zadnji grubi građevinski radovi. "Sad smo već u fazi da pokrećemo opremanje proizvodne hale s raznom opremom", rekao je Rimčev šef strateških projekata.
Kampus će se prostirati na 200 tisuća kvadrata, dok će sama površina uredske i proizvodne zgrade iznositi oko 100 tisuća kvadrata.
"Cijela proizvodna zgrada je veća od povijesnog centra Dubrovnika, 200 puta 400 metara", rekla je Marta Longin, šefica marketinga i komunikacija.
Zajedno s dovršetkom kampusa tvrtka uvodi i automatizaciju i industrijalizaciju u proizvodne procese.
U zgradu na Jankomiru, bivši Pevec, Rimac Automobili su uložili oko 7 milijuna eura. Nakon preseljenja tvrtke u kampus ovaj pogon ipak neće biti napušten. U njemu će ostati dio proizvodnih linija čiji rad se ne može prekidati. Prostor će služiti i za postprodajne usluge.
"U Francuskoj, u Bugattiju, je tzv. after-sales dva ili tri puta veći od dijela za proizvodnju. Očekujemo velike prihode od te postprodaje", kaže Brkljačić.
"Neće postojati Bugatti-Rimac auto"
"Spajanje s Bugattijem je bila pobjeda za sva strane, Volkswagen, Porsche, za nas i naše zaposlenike. Ujedinili smo dva brenda, Rimac i Bugatti. Rimac je donio svježinu, mi nismo opterećeni velikim sustavom i nastojimo zadržati fleksibilnost. Bugatti donosi 113 godina iskustva u izradi takvih automobila", rekla je Marta Longin, voditeljica marketinga i komunikacija.
Cilj je, kaže Longin, napraviti svjetski vodeću hiperautomobil kompaniju i obarati nove rekorde.
"Neće postojati Bugatti-Rimac auto, imamo različite vizije za oba brenda", naglasila je Longin.

bi Vas mogao zanimati
Izdvojeno
Pročitajte još
bi Vas mogao zanimati